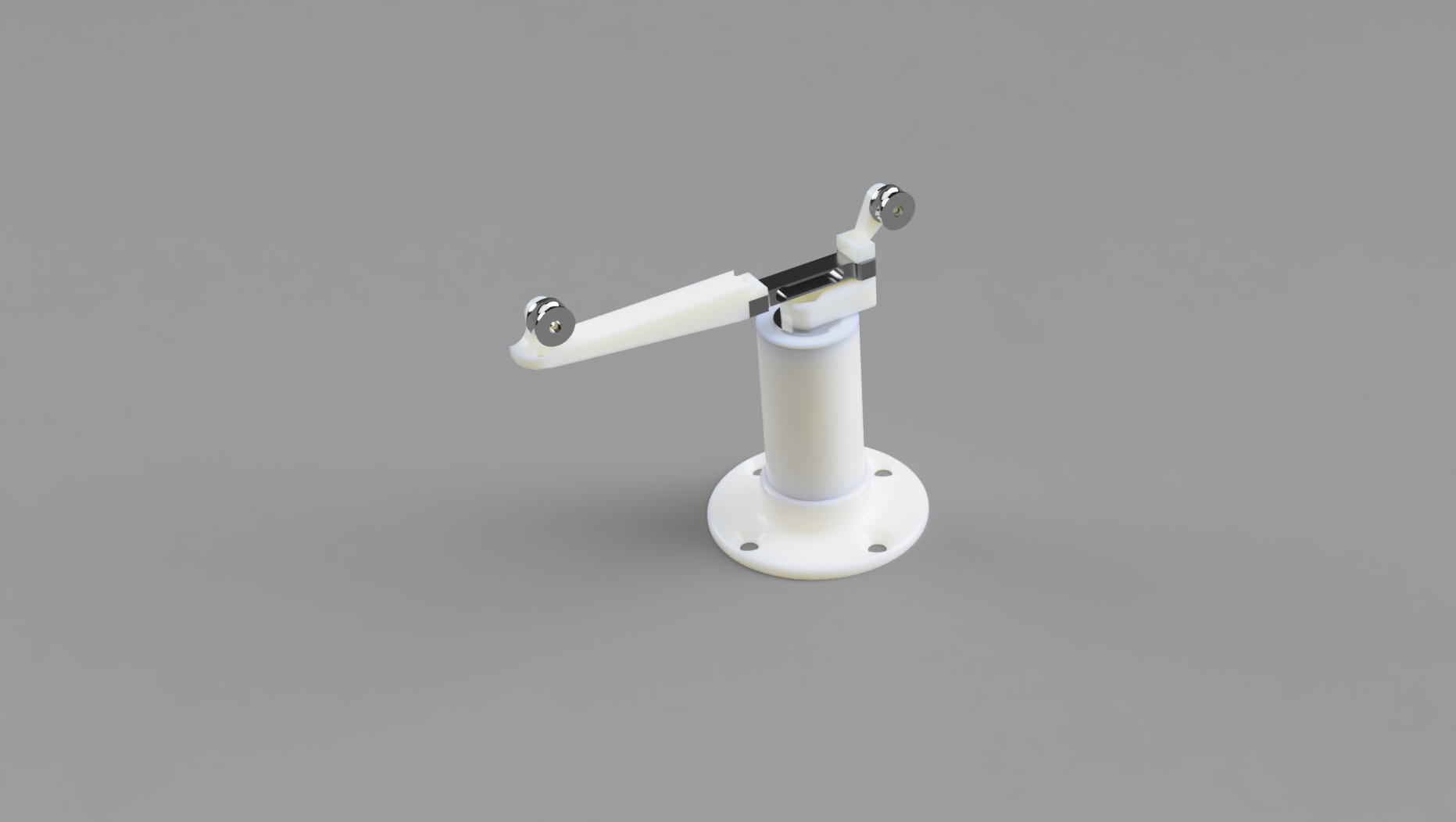
A Dynamic Hindlimb Unloading Apparatus
Hindlimb Unloading Model of Microgravity (see Gnyubkin and Vico, 2015).
Load on Forelimbs (left, black) and Tension on Tail (right, red) versus Angle of Head-down Tilt. Equations are my own, dotted lines are best fit (recreated from Hargens et al., 1985).
Introduction
The hindlimb unloading (HU) model has been used to simulate microgravity—and more broadly, disuse—for over 40 years (E. Morey-Holton et al., 2005; E. R. Morey-Holton & Globus, 2002). Since the National Aeronautics and Space Administration (NASA) confirmed similar tissue fluid shifts and musculoskeletal responses in rodents compared to subjects in the weightlessness of space, HU has become an important model to study other physiologic factors relating to metabolic, endocrine, and adrenal function. However, the current (and common) HU apparatus is statically calibrated, such that the hind-limbs are unloaded through tail suspension using a constant force. This weight is typically equal to a 30° incline (i.e. head-tilt down) which matches the cephalic fluid shift and pressures experienced in zero-G (Hargens et al., 1985) while providing normal weight-bearing on the forelimbs and unloading the lumbar vertebrae but not the cervical vertebrae. Since tilt-angle and weight-unloaded are co-linear, the notion that a standard unloading protocol could be implemented dynamically is possible if the unloaded weight could be monitored. A dynamic HU apparatus would allow real-time modulation of fluid shifts and thereby enable investigation of acute, temporally-precise investigation of physiology and neural activity. Here, I explore the design of a dynamic HU apparatus using a calibrated and closed-loop load cell fed-back to a motor controlling the hind-limb unloaded weight. Coordinated neural recordings may make possible first-of-their-kind, causative demonstrations of microgravity-induced neural adaptations.
Other Reading
-
An Alternant Method to the Traditional NASA Hindlimb Unloading Model in Mice (Ferreira et al., 2011)
Design Concept
Early Hindlimb Unloading Cage (see Wronski & Morey-Holton, 1987)
The most common HU design augments a rodent home cage with a low-friction, X-Y-style track to allow free movement. This design requires that animals be weighed using a special balance that unloads animals to the same degree as the cage. Issues with this design include the possible use of nest material built to reduce the intended hindlimb load and cumbersome re-calibration of the unloaded weight.
If hindlimb load is constantly being measured, a dynamic loading system removes the need for the X-Y track. To perform load measurements, a load cell can be used that utilizes an internal Wheatstone bridge to translate physical deflection into differential voltage. This type of load cell is typically used for scales; they are a rigid aluminum-alloy with an IP65 rating (“dust tight” and water-resistant) and can measure grams to kilograms.
Mechanics
This concept is based on a swiveling crane where the load is measured via the load cell which makes a beam through the swiveling arm. The height is set by a standard 1” PVC tube which uses a flange bearing to achieve the swiveling action. A tensioned line runs from a ground-mounted stepper motor through two frictionless pulleys and is finally guided through a single through-hole into the space (or cage) below. The custom parts shown can be 3D printed in roughly 90 minutes using PLA material and are assembled using standard metric hardware (see BOM below). Parts were designed and rendered in Fusion 360, sliced in Prusa Slicer, and printed on a Prusa Mini.
Control System
Load bearing is continuously sampled from an Arduino Every Nano connected to an ADS1115 differential ADC module communicating over I2C. The control of a NEMA 17 motor is accomplished through a 4-wire stepper motor library and external stepper motor controller (prototype code on Github). The system works in the same manner as a thermostat: the motor keeps constant tension on the unloading line with some error to eliminate feedback oscillations.
Calibration Procedure
-
After the system is turned on, use the buttons to tension the line (moves up/down).
-
Press both buttons together to save the tension set-point (this can be done at any time).
The stepper motor allows for roughly 0.3mm precision in the configuration shown. However, the limiting factor on precision is in the details of the feedback regulation and timing, such that the system is neither too reactive nor too sluggish.
Bill of Materials
Below is the minimum BOM for 1 apparatus, but notice some parts are kits, enough to build n, so the total cost at quantity is significantly reduced. 3D parts are not listed as they are negligible with access to a 3D printer.
Future Directions
One of the biggest traps for smart engineers is optimizing something that shouldn’t exist. -Elon Musk
The utility of this HU apparatus is entirely in its ability to provide dynamic load control while recording time-varying physiological parameters, although its low cost, portability, and minimal construction may make it valuable to any HU paradigm. For example, load profiles could be programmed into the control system and cued on demand while neural activity is recorded in order to answer how the brain immediately responds to dynamic microgravity conditions. Dynamic loading could also be coordinated with sleep states to understand the relationship between load and sleep architecture (H0: slow-wave sleep intensifies with reduced loading).
If this project becomes useful to my broader research goals (or yours) the parts and control system will be consolidated and open-sourced. If you are interested in testing, let me know with an email or comment. So, todo:
-
Refined control system
-
Transition to BLE-enabled microcontroller
-
Consolidate electronics into low-cost PCB
-
Add calibration protocol and display to show real-time load
-
-
Test in real conditions
-
Implement safety features (zero-load detection)
-
Addendum
Recent Comments
Archives
- April 2023
- January 2023
- November 2022
- May 2022
- March 2022
- January 2022
- December 2021
- April 2021
- December 2020
- October 2020
- August 2020
- July 2020
- March 2020
- February 2020
- January 2020
- December 2019
- November 2019
- October 2019
- January 2019
- December 2018
- November 2018
- August 2018
- July 2018
- April 2018
- March 2018
- November 2017
- October 2017
- February 2017
- October 2016
- August 2016
- July 2016
- November 2015
- October 2013
- February 2013
- January 2013
- August 2012
- July 2012
- June 2012
- May 2012
- April 2012
- February 2012
- December 2011